CMMS
Tips to Simplify Inventory Management with Maintenance Control Software
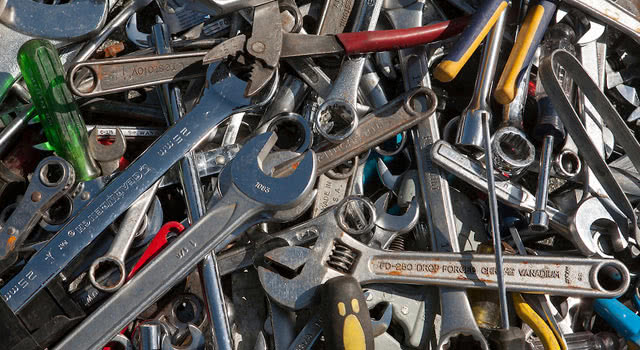
Maintenance management systems have become an essential tool for modern-day maintenance organizations. Maintenance control software enables organizations to record, manage and communicate their day-to-day operations. The software typically comes equipped with an inventory control module, which is used to track stocked, un-stocked and special order items that are moved in and out of inventory. It may also be capable of tracking the following:
- Vendors
- Purpose of items
- Location of items
- Cost of items
- Availability
- Substitute items that can be used
- Inventory turnover
- Minimum/maximum management
- Equipment using items
Effective inventory management is one of the best ways to accelerate the ROI of your CMMS implementation. Tracking inventory, however, can be a complex and daunting task. Organizations have to track a variety of equipment, as well as the spare parts and tools used to properly maintain that equipment.
For a long time organizations had to do inventory management manually. The difficulty of tracking inventory in different quantities and with varying characteristics gets magnified when manual procedures are used. An inventory control module can simplify inventory management through better record keeping and automated reporting. Unfortunately, inventory management modules are often underused.
Many maintenance managers mistakenly assume that inventory management comes as an automatic function of maintenance management systems, but maintenance software can only simplify and automate a process that’s already effective.
Optimizing Inventory Management with a Maintenance Management System
Effective inventory tracking has a direct impact on your organization’s bottom line. An inventory tracking system tracks products and materials anywhere in your manufacturing plant or facility in real time. You can even use barcode technology to identify materials at any location.
An inventory control module also streamlines requests, controls costs and reduces inventory shrinkage and dead inventory. Advancements in mobile technology have made it possible to manage and track inventory with mobile devices.
Key Performance Indicators (KPIs) for Inventory Control
Modern maintenance management systems boast powerful tools that stakeholders can use to track and analyze the extensive data available. A dashboard that visually represents multiple KPIs allows you to keep a finger on the pulse of your organization, set targets, monitor results and improve efficiency. Examples of measures related to inventory management are parts at reorder point, service level, inventory turnover and slow moving parts. An easy-to-read dashboard simplifies how you access the information needed to make decisions.
DPSI maintenance management systems help organizations effectively manage the ordering, purchasing and management of inventory to ensure uninterrupted operations. DPSI’s maintenance control software can help you reduce spare parts inventory, prevent downtime by securing spare parts, control purchase order processes and make the most of your budget. Contact us today or sign up for a free trial to learn how our maintenance software can make a difference in your organization.